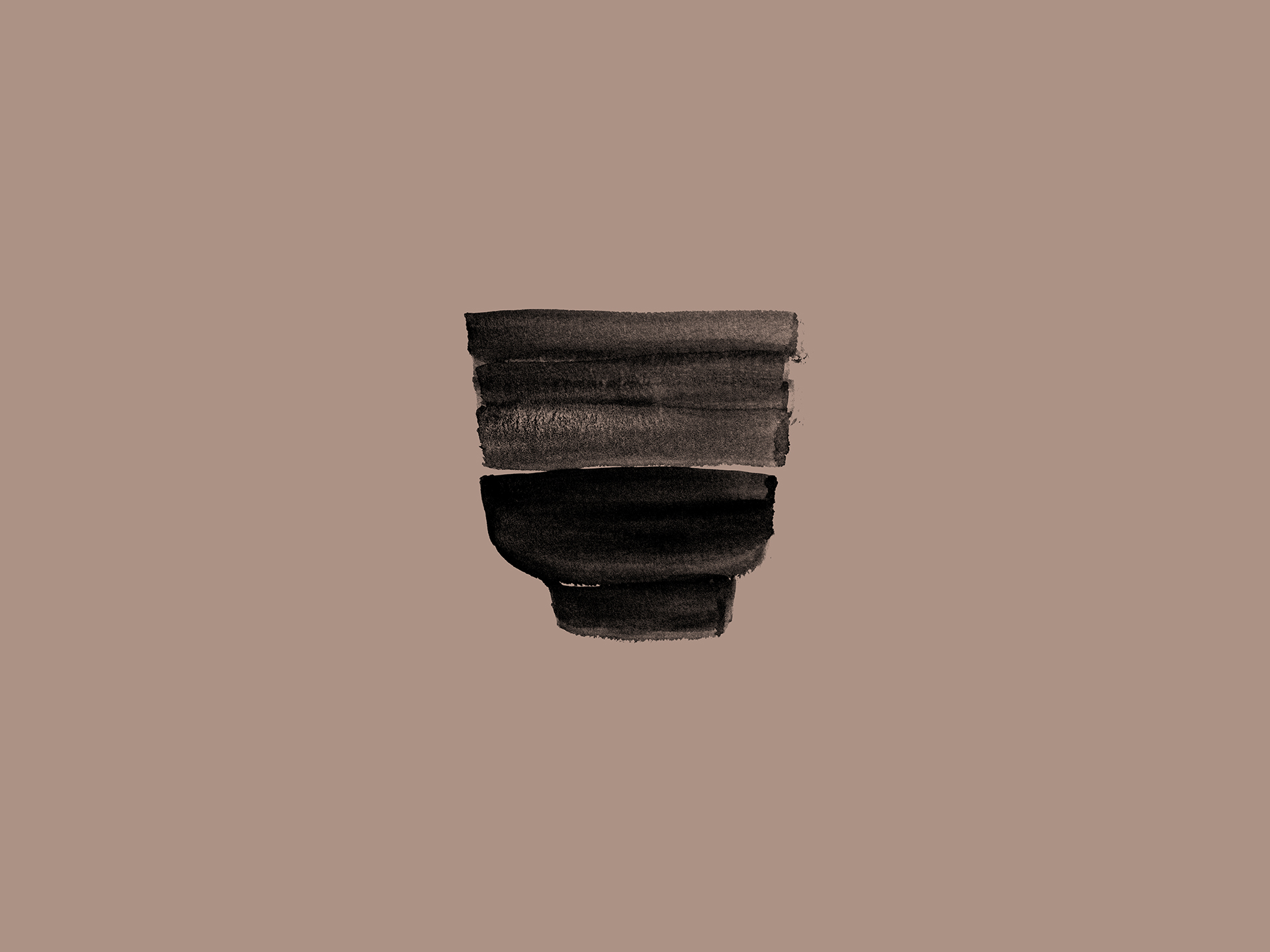
Design House Stockholm is a publishing house for creators and designers with a Scandinavian design expression. Although furniture, lighting and carpets are the fastest growing part of the publishing house, we this time present how the kitchen and the tableware will develop in our collaboration with Carina Seth Andersson and Matti Klenell.
Anders Färdig's (Founder & CEO) story about the design process: It is exciting to follow some of Sweden's most interesting designers. The client was the National Museum. The museum is already filled to the brim with things for the table from many centuries. Now we can participate in creating porcelain and glass from 2019. Carina Seth Andersson designs the tableware, Matti Klenell draws glass and we make sure that all the necessary ingredients in the production are available so that the small details in shape and function are allowed to shine.
Think about it, how often do you choose
something that you should use every day,
several times, year in and year out?
When you choose utility items for the table set, a well-designed more beautiful everyday item will often not be to your advantage until you have used it for a while. Simple functional basic forms will be your favorite cup, favorite porcelain or your favorite glass.At Design House Stockholm we have been developing glass, porcelain, cutlery and kitchenware since day one (1992). Before that, I developed collections for companies such as Kosta Boda, Rörstrand, Gense, Boda Nova and Höganäs Ceramics.
When Carina started to form her thoughts, the specific requirements sounded something like this: stoneware, high-burnt, thin (so thin it just goes without skew), glossy glaze (where the food is located), matte surface showing the mass of the stoneware untreated (where you grip bowls and cups) , a small mark somewhere reminiscent of the origin of the tableware.
Time for production: Each product is designed to match the requirements of the stoneware mass on how it wants to be shaped. The mass we selected is also used to produce grating molds that can withstand insertion into high temperature ovens. In other words, all products in the tableware can withstand insertion into the oven at high temperature (obviously the tableware can withstand microwave and dishwasher).
The color of the mass can be a concern. It is not obvious that the mass has a beautiful soft sand color as in this case. Often, the stoneware is allowed to have a covering glaze as the color of the stoneware varies. Now Carina wanted to show the raw stonework when the mass "glows".
There were a couple of "porcelain nerds" sitting in Design House Stockholm's office studio one year ago. How would the small brand NM& be put on the goods? Creative magnetism we call it when everyone's thoughts are allowed to fly freely in the room and then land in a solution that would never come to fruition unless the group met.
So, the idea of labeling was born. NM& would be engraved just like in stone. With the help of laser technology, you can "engrave" through the transparent glaze to get the raw stoneware visible through the mark. Carina Seth Andersson pondered for a few days and then decided. So now NM& is engraved in stone (ware) for all time.
A little about the practical thoughts on the tableware; The cups are available with and without handles. If you choose without, the cup/mug can have several uses. The mini-dish before or after the main course is advantageously served both hot or cold out of these. The small saucer for the cups is without a foot ring to also function as a mini plate. For those who cook Asian cuisine, these small plates are perfect.
When we got sketches on the glass from Matti Klenell it was said that the glass would be manufactured in press glass. The glass then gets a stitch, becomes a little thicker but also more durable. The idea was also to make the glass in clear glass, smoked and amber. To bring life to the colors, however, it would be much more beautiful to make the glasses by hand. You can then blow the glasses thinner. Matti asked for samples in a mouth-blown versions, provided that the price was not too high and that the quality would withstand restaurant management. Afterwards, we can see that the glass met all of Matti's high standards except one. The number of visitors to the National Museum Restaurant was huge. The pressure on serving trolleys and dishwasher trays became too much. For home use, the durability of the glass has no problems but in tough restaurant management a hardened machine-made glass is required.
In the traditional glass production, the top of the glass was blasted after the glass passed through the cooling tube. Then you got the most comfortable edge to drink from. Matti's glass is manufactured raw. In order to get the vivid shifts in the colored glasses, a technique called undercutting is used. Before blowing out the glass in molds you first catch colored glass and then put on clear glass and then blow out the glass to its definite shape. You will notice that each colored glass shifts slightly in strength. Accept this as a sign of craftsmanship. Most of the colored glass on the market is manufactured in machines in clear glass and then spray painted externally. The disadvantage of these glasses is that the outside can be easily scratched and that the surface mats with time. The Unda glass is stackable with its characteristic waist. However, you should not stack more than three glasses.
Anders Färdig
Founder & CEO